Catering Equipment
We provides Industrial Machines, Machinery Equipment and Parts directly to the consumer. The company is web based and operates throughout the Australia and New Zealand.
Conventional Lifting
Hand hoists have chain, rope, and cable models, the former being a safer alternative. It is also more reliable to lift heavy materials. Its strength from the solid-steel build and linked chain eases the pressure of sustaining heavy weight.
Drum Lifting in Warehousing
Drum lifting necessitates the usage of a forklift. In warehousing, weights as much as 3000kgs or more need to be transferred or shifted, at a time. Drum grabs use clamps that tightly hold the drum at its top before lowering it.
Showing posts with label Australia. Show all posts
Showing posts with label Australia. Show all posts
2:20 AM
Tanker trucks are motorized vehicles designed to carry liquefied loads, dry bulk cargo or gases on roads. They are also called tank trucks, petrol trucks, or simply trucks. Tank trucks vary in size, but the one mainly used, and most common tanker truck for sale is the large version of it. Large tank trucks have the capacity of 20,800 to 43,900 L. By shape, they are mainly cylindrical, except for the ones that have to be complied with food regulations, refrigeration capability and pressurization capability. Tanker truck's main purpose is to transfer liquids such as gasoline, petrol, diesel, milk, juices, wine, water and industrial chemicals. Depending on the liquid they carry, they can be made of aluminum, carbon steel, stainless steel or fiberglass.
Before putting any liquid in the tank, especially in one you bought at a tanker truck for sale section, you must disinfect it. Even if it's a completely new and unused tank, if you are going to put a liquid for drinking in it, you must clean it first. Every time a liquid stays for a longer period in a tank, it contaminates it. For example milk, wine and even water can easily contaminate the tank. The easiest and most commonly used way to disinfect a tank is by using chlorine.
There are two forms of chlorine substances you can use for disinfecting: calcium hypochlorite and sodium hypochlorite. Using any of them, a 0.2% solution has to be made. Next, you spray the tank with the solution and close it. Leave the tank for at least 4 hours, or through the night, and wash it in the morning. After this, you can put the liquid in. Calcium hypochlorite comes as white granules and can be bought in a pharmaceutical store. It contains 50-70 % chlorine, and is much stronger than liquid bleach. In addition, you can test the tank for bacteria. Testing for bacteria should be done at least once a month. If after disinfection, the water is still contaminated, consider chlorinating every load, or changing the source of water.
Why is it so important to disinfect a tanker truck
Monday, April 27, 2015
Tanker trucks are motorized vehicles designed to carry liquefied loads, dry bulk cargo or gases on roads. They are also called tank trucks, petrol trucks, or simply trucks. Tank trucks vary in size, but the one mainly used, and most common tanker truck for sale is the large version of it. Large tank trucks have the capacity of 20,800 to 43,900 L. By shape, they are mainly cylindrical, except for the ones that have to be complied with food regulations, refrigeration capability and pressurization capability. Tanker truck's main purpose is to transfer liquids such as gasoline, petrol, diesel, milk, juices, wine, water and industrial chemicals. Depending on the liquid they carry, they can be made of aluminum, carbon steel, stainless steel or fiberglass.
Before putting any liquid in the tank, especially in one you bought at a tanker truck for sale section, you must disinfect it. Even if it's a completely new and unused tank, if you are going to put a liquid for drinking in it, you must clean it first. Every time a liquid stays for a longer period in a tank, it contaminates it. For example milk, wine and even water can easily contaminate the tank. The easiest and most commonly used way to disinfect a tank is by using chlorine.
There are two forms of chlorine substances you can use for disinfecting: calcium hypochlorite and sodium hypochlorite. Using any of them, a 0.2% solution has to be made. Next, you spray the tank with the solution and close it. Leave the tank for at least 4 hours, or through the night, and wash it in the morning. After this, you can put the liquid in. Calcium hypochlorite comes as white granules and can be bought in a pharmaceutical store. It contains 50-70 % chlorine, and is much stronger than liquid bleach. In addition, you can test the tank for bacteria. Testing for bacteria should be done at least once a month. If after disinfection, the water is still contaminated, consider chlorinating every load, or changing the source of water.
12:12 AM
3 Benefits Of Compact Excavator
Wednesday, August 20, 2014
The compact excavators are described as extremely efficient and versatile machines, designed to be used for different tasks. In my opinion, their versatility comes from the different excavator attachments. With compact size and with a wide range of excavator attachments, these machines offer many benefits and advantages.
Click here to see some of them.
Click here to see some of them.
Labels:
Attachments,
Australia,
Construction,
Equipment,
excavator,
Implements,
machines,
Sale
11:28 PM
What Are The Most Used Bulldozer Attachments
Wednesday, July 30, 2014
A bulldozer is a vital piece of equipment, especially in the construction industry. It is used for a variety of applications, including cleaning debris, concrete, steel poles and others. The bulldozer is large in size and features two big wheels, specialized for heavy-duty applications. So, the bulldozer is able to perform the most difficult tasks on the most difficult terrains. The only problem of the bulldozer is that it can not travel on a longer distances, but only maneuver around a job site. However, the versatility and flexibility of the bulldozer can be further increased by adding the right bulldozer attachment for specific application. Here are the most used bulldozer attachments and their respectful manufacturers.
Grouser – Grouser is a reliable bulldozer attachment manufacturer that offers a full range of attachments. The most popular bulldozer attachment by Grouser is the 6-way dozer blade, coming in widths from 1.8m to 2.8m. Made from heavy-duty components, the Grouser dozer blade is the ideal bulldozer attachment for cleaning all types of materials.
Weldco-Beales – Weldco-Beales is most known for its bulldozer attachment D11 blade. It is a widely utilized dozer blade in oil sands environments, thanks to its unique design. Speaking of its design, it provides much more benefits, such as reduced wear on the surface of the blade and its cutting edges, better material handling and reduced fuel consumption.
AIM – The well-known attachments manufacturer and provider has gained a lot of attention with the AIM HD60 bucket, that features AR400 steel tines. This bulldozer attachment is specifically designed with a curved design that provides reduced ground resistance and allows for easy clean-out. Reinforced with dual gussets for better stability, this bulldozer attachment comes in few configuration with different capacities.
Solesbee – Solesbee is a manufacturer of various attachments for different machines. However, its dozer rake with brush guard is an exceptional bulldozer attachment, which enables the bulldozer to operate the most demanding applications, such as raking brush, piling trees, limbs and land clearing applications. Made of high-quality with high performance, the Solesbee dozer rake is available for any bulldozer model.
Vail Products – Rippers by Vail Products make the bulldozer much more efficient, as they break up subsoil materials for the next pass. Built to last and withstand all conditions, the Vail Products' rippers enhanced the productivity on any job site and require only minimum maintenance. They are mounted on the frames or buckets and are commonly recognized for their universal bolt-on hitch, durability and toughness.
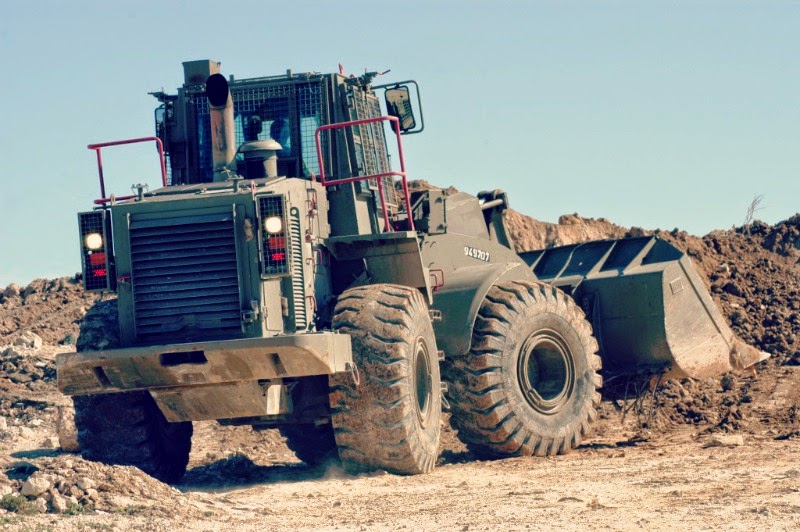
Grouser – Grouser is a reliable bulldozer attachment manufacturer that offers a full range of attachments. The most popular bulldozer attachment by Grouser is the 6-way dozer blade, coming in widths from 1.8m to 2.8m. Made from heavy-duty components, the Grouser dozer blade is the ideal bulldozer attachment for cleaning all types of materials.
Weldco-Beales – Weldco-Beales is most known for its bulldozer attachment D11 blade. It is a widely utilized dozer blade in oil sands environments, thanks to its unique design. Speaking of its design, it provides much more benefits, such as reduced wear on the surface of the blade and its cutting edges, better material handling and reduced fuel consumption.
AIM – The well-known attachments manufacturer and provider has gained a lot of attention with the AIM HD60 bucket, that features AR400 steel tines. This bulldozer attachment is specifically designed with a curved design that provides reduced ground resistance and allows for easy clean-out. Reinforced with dual gussets for better stability, this bulldozer attachment comes in few configuration with different capacities.
Solesbee – Solesbee is a manufacturer of various attachments for different machines. However, its dozer rake with brush guard is an exceptional bulldozer attachment, which enables the bulldozer to operate the most demanding applications, such as raking brush, piling trees, limbs and land clearing applications. Made of high-quality with high performance, the Solesbee dozer rake is available for any bulldozer model.
Vail Products – Rippers by Vail Products make the bulldozer much more efficient, as they break up subsoil materials for the next pass. Built to last and withstand all conditions, the Vail Products' rippers enhanced the productivity on any job site and require only minimum maintenance. They are mounted on the frames or buckets and are commonly recognized for their universal bolt-on hitch, durability and toughness.
Labels:
Attachment,
Attachments,
Australia,
Bulldozer,
Business,
Construction,
dozer,
Equipment,
Implements,
Industry,
Machinery,
machines,
Sale,
tools
12:49 AM
Attachments for Bobcat Loaders
Tuesday, July 29, 2014
Bobcat is a leading industry
manufacturer and world-known brand that produces high quality,
durable and powerful loaders. The brand also offers loader
attachments that can be matched with more than 60 different
applications. Loader attachments are designed and manufactured to
perfectly fit the base machine, which optimizes job performance,
dependability and durability. Fast and secure loader attachments
change is guaranteed by an exclusive mounting system. Loader
attachments even add more versatility when used with Bobcat loaders.
Here are some of the more commonly used Bobcat loader attachments.
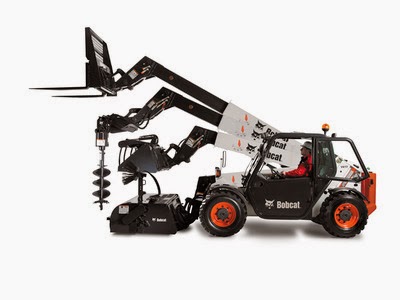
Backhoe attachment - With a backhoe
attachment you will be able to transform your bobcat loader into a
powerful excavator. With a full line of models, backhoe attachments
can be fitted with any Bobcat loader size. Perfect for tasks such as
landscaping, nursery sites, water and power maintenance lines, etc,
Bobcat backhoe attachment due to its minimal ground disturbance
operation, is also ideal for work in sensitive areas. The backhoe
attachment can be switched easy and fast. Its unique mounting system
maximizes the performance and minimizes the downtime.
Bucket Construction/Industrial - Fair
cutting edge visibility and excellent bucket breakout force are just
some of the features offered by construction and industrial buckets
in order to guarantee better digging and easier bucket filling. It is
an ideal loader attachments for tough digging and material handing.
Bucket (Rock) - Bucket (rock) is
designed for tough working conditions, and its tines are designed to
provide strength and durability. Ideal for contractors and
landscapers who want to separate unnecessary objects, like rocks and
debris while leaving finer material behind on the job site.
Grapple (Industrial) - Developed for
maximum power and reliability. The two-arm design provides strong,
even biting force. It can handle onto the toughest materials in the
industrial or construction setting. Easy operation and secure handle
bulk and uneven loads are allowed by its hydraulic controls. The
versatility on choosing a bucket or a fork bottom will maximize load
capability.
Grapple (Root) – This type of grapple
is designed to perform a smooth, yet strong operation with maximum
chomping and ripping power to complete even the toughest jobs. Also
with its specific tooth design, materials can be picked without
driving the teeth into the ground. Ideal for landscaping, demolition,
construction and grounds maintenance.
With the versatility of Bobcat loader
attachments, you will be able to grow you business, replace
non-efficient machines and have the necessary tools to accomplish
major projects.
Labels:
Attachments,
Australia,
Bobcat,
Business,
Construction,
Equipment,
Implements,
Machinery,
machines,
tools
1:07 AM
Different Types of Mobile Crushers
Friday, July 18, 2014
Mobile crusher or commonly known as mobile crushing plant is a crushing machine, especially suitable for crushing and recycling directly on-site. The fixed crushers are very efficient crushers, but the mobile crushers benefit from their mobility. The mobile crushers can get from one job site to another and easily move around a job site. However, all known crushing machines, such as jaw crusher, cone crusher, roll crusher and impact crusher, are being modified to mobile, by adding tracks or wheels. Some crushers are made to be towed by a purpose vehicle, which is also an innovative and mobile solution. Here are some types of mobile crushers.
Mobile Crushing Plant – The mobile crusher or mobile crushing plant is a large piece of crushing and screening equipment, which combines conveying, screening and crushing processes. Usually, the maximum feeding size is about 1500 mm and has a maximum production capacity of 500 t/h. The mobile crushing plant is suitable for crushing and disposal of construction waste, railway, highway and many other projects. The design of the mobile crushing plant is so that it can completely adapt to all mobile crushing requirements and reduce the operation costs. The mobile crushing plant usually comes with vibrating feeder, cone crusher, jaw crusher, impact crusher and belt conveyor.
Crawler Mobile Crusher – The crawler mobile crusher has a maximum production capacity of 450 t/h and plays a big role in many applications, including quarry, mining, quartz sand, dry mortar, concrete mixing and coal exploiting applications. It is identical with the mobile crushing plant, with the difference of using tracks, not wheels. The crawler mobile crushing plant has the advantages of being light in weight, compact size, ability to work in narrow spaces, reliable operation and provides fuel savings.
Mobile Jaw Crusher – Mobile jaw crusher is a crushing machine used for primary crushing, with a maximum input size of 1000 mm. It is able to process iron ore, gold ore, manganese ore, limestone, basalt, rocks, marble, river stone, gravel and many others. The jaw crusher usually uses wheels, so it is suitable for the mining, quarry, mixing, building, railway and many other applications. The jaw crusher has a high-capacity and provides the operators with a reliable and very efficient operation.
Mobile Cone Crusher – Mobile cone crusher is a secondary crusher and is known for its high-performance. This secondary crusher is widely used in the mining, quarry, mixing and building construction industry, for processing iron, copper, gold, manganese, limestone, granite, gravel, coal, marble, rocks, quarts and many other materials. Thanks to its lightweight and compact design, the cone crusher provides an incredible crushing performance.
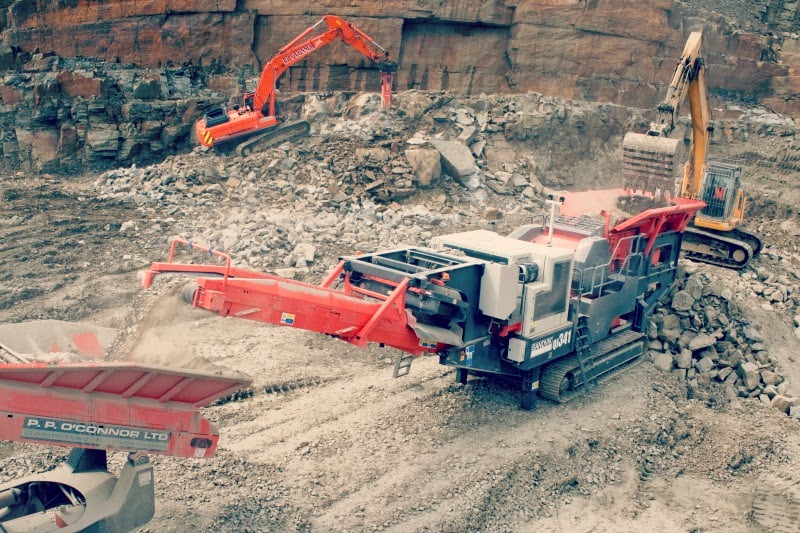
Mobile Crushing Plant – The mobile crusher or mobile crushing plant is a large piece of crushing and screening equipment, which combines conveying, screening and crushing processes. Usually, the maximum feeding size is about 1500 mm and has a maximum production capacity of 500 t/h. The mobile crushing plant is suitable for crushing and disposal of construction waste, railway, highway and many other projects. The design of the mobile crushing plant is so that it can completely adapt to all mobile crushing requirements and reduce the operation costs. The mobile crushing plant usually comes with vibrating feeder, cone crusher, jaw crusher, impact crusher and belt conveyor.
Crawler Mobile Crusher – The crawler mobile crusher has a maximum production capacity of 450 t/h and plays a big role in many applications, including quarry, mining, quartz sand, dry mortar, concrete mixing and coal exploiting applications. It is identical with the mobile crushing plant, with the difference of using tracks, not wheels. The crawler mobile crushing plant has the advantages of being light in weight, compact size, ability to work in narrow spaces, reliable operation and provides fuel savings.
Mobile Jaw Crusher – Mobile jaw crusher is a crushing machine used for primary crushing, with a maximum input size of 1000 mm. It is able to process iron ore, gold ore, manganese ore, limestone, basalt, rocks, marble, river stone, gravel and many others. The jaw crusher usually uses wheels, so it is suitable for the mining, quarry, mixing, building, railway and many other applications. The jaw crusher has a high-capacity and provides the operators with a reliable and very efficient operation.
Mobile Cone Crusher – Mobile cone crusher is a secondary crusher and is known for its high-performance. This secondary crusher is widely used in the mining, quarry, mixing and building construction industry, for processing iron, copper, gold, manganese, limestone, granite, gravel, coal, marble, rocks, quarts and many other materials. Thanks to its lightweight and compact design, the cone crusher provides an incredible crushing performance.
12:01 AM
What To Consider When Choosing Wheeled Excavator
Monday, July 14, 2014
The wheeled excavator is a flexible and versatile machine, with a very efficient and reliable operation. Since they are very popular and efficient, the contractors may face a wide range of wheeled excavator models, requiring to do a deeper and extensive research. When buying a wheeled excavator, you must make sure that its specification will meet the requirements of the application. You have a broad range of factors to consider, such as weight, capacity, outreach, size, tail swing, auxiliary hydraulics, shape, horsepower, breakout force, attachments and many more. Whether renting or buying, you need to make sure that the specifications of the wheeled excavator matches up to the application.
The first consideration is to make sure that the wheeled excavator you are about to buy or rent has enough capacity to lift the materials you need. Also, the auxiliary hydraulics are required to run a variety of attachments. Most operators purchase a wheeled excavator with 3 to 5 attachments and the most common are a hydraulic thumb, a bucket and a breaker. The attachments are very important if you plan to use the excavator on a daily basis, so consider which ones you want included. The transportation is not an issue with the wheeled excavator, since it has its own wheels to get whenever is needed.
The size and weight of the wheeled excavator are also important factors you should consider. To do so, you can specify the type of application or range of applications. The tail swing must be accounted and must be reduced, if the application gets the wheeled excavator close to the material. And of course, you should consider the comfort in the cabin, of which the productivity depends to a significant extent. It may seem simple, but to choose a cabin that suits the application best, with correctly positioned door, stairway and great field of visibility and provides you with comfort in the same time, is very difficult.
When choosing a wheeled excavator you should not only look on horsepower, because there are many more important factors to consider. There are some wheeled excavator models with less horsepower than another one, but perform much better because of its hydraulic system. Unfortunately, many contractors are not aware of that that and go for a wheeled excavator with a big amount of horsepower. If you have not made your decision yet, consider all these factors mentioned above and you will have the best wheeled excavator.
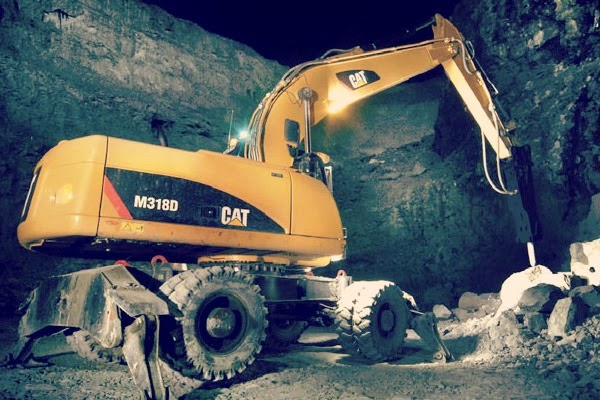
The first consideration is to make sure that the wheeled excavator you are about to buy or rent has enough capacity to lift the materials you need. Also, the auxiliary hydraulics are required to run a variety of attachments. Most operators purchase a wheeled excavator with 3 to 5 attachments and the most common are a hydraulic thumb, a bucket and a breaker. The attachments are very important if you plan to use the excavator on a daily basis, so consider which ones you want included. The transportation is not an issue with the wheeled excavator, since it has its own wheels to get whenever is needed.
The size and weight of the wheeled excavator are also important factors you should consider. To do so, you can specify the type of application or range of applications. The tail swing must be accounted and must be reduced, if the application gets the wheeled excavator close to the material. And of course, you should consider the comfort in the cabin, of which the productivity depends to a significant extent. It may seem simple, but to choose a cabin that suits the application best, with correctly positioned door, stairway and great field of visibility and provides you with comfort in the same time, is very difficult.
When choosing a wheeled excavator you should not only look on horsepower, because there are many more important factors to consider. There are some wheeled excavator models with less horsepower than another one, but perform much better because of its hydraulic system. Unfortunately, many contractors are not aware of that that and go for a wheeled excavator with a big amount of horsepower. If you have not made your decision yet, consider all these factors mentioned above and you will have the best wheeled excavator.
Labels:
Attachments,
Australia,
Business,
Equipment,
excavator,
excavators,
Horsepower,
Machinery,
machines,
mining,
Sale,
tools,
Wheeled
Location:
Melbourne VIC, Australia
1:28 AM
A Brief History Of Cone Crusher
Tuesday, July 8, 2014
A cone crusher is a type of crushing equipment able to crush all types of medium-hard mineral rocks and stones. The cone crusher offers many advantages over the other crushing machines, such as low energy consumption, reliable and efficient operation and a high crushing ratio. Despite being used in many industries, it is most commonly used in the construction and the mining industry. With the rapid development of the construction and mining machines, the cone crusher is being modified constantly in order to become the perfect crushing tool. However, it has not always been a common crushing tool. Continue through this article and learn something about the history of the cone crusher.
The first cone was developed in USA in 1878 and put in use in the next year. However, many believe that the original design of the cone crusher known today is a copy of the former Soviet union spring type cone crusher. Despite those rumors, Milwaukee Symons brothers are believed to be the designers and inventors of the spring cone crusher, so it is known as Symons cone crusher. By the end of the 19th century, USA began to use the cone crusher increasingly. After many years of constant development and research, the under pressure problem of the spring cone crusher was solved and today the cone crusher is one of the most efficient crushing machines.
The first hydraulic cone crusher was developed in 1948 by an American company. This cone crusher is able to expel some uncrushable materials that have somehow entered the crushing chamber and its discharging gap is adjustable. Until 1970s, an automatic controller was developed and featured in the hydraulic cone crusher. This was only the beginning. Through the following years, the cone crushers was significantly improved in all terms; efficiency, features, technologies, energy consumption, maintenance costs, etc.
Today, there are many different types of cone crushers, of which every type is most suitable for a specific range of applications and materials. The importance of this type of crushing machine has significantly increased, because of its effectiveness and surprisingly low operating costs. The cone crusher is able to crush hard, medium-hard and many different types of materials, while providing a reliable and efficient crushing operation. When compared with the jaw crusher, the cone crusher has a more stable structure, higher efficiency, economical operation and is adjustable, unlike the jaw crusher. Flexible and efficient, the cone crusher is widely utilized in many various industries.
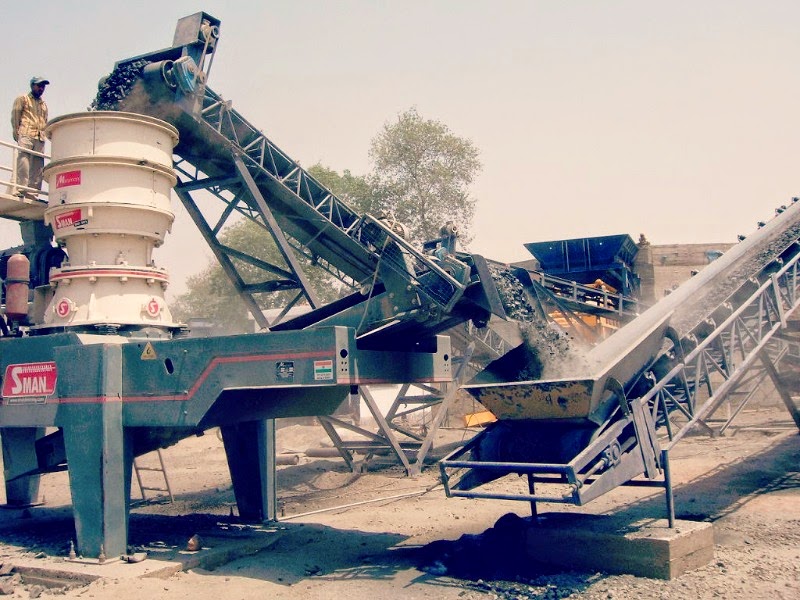
The first cone was developed in USA in 1878 and put in use in the next year. However, many believe that the original design of the cone crusher known today is a copy of the former Soviet union spring type cone crusher. Despite those rumors, Milwaukee Symons brothers are believed to be the designers and inventors of the spring cone crusher, so it is known as Symons cone crusher. By the end of the 19th century, USA began to use the cone crusher increasingly. After many years of constant development and research, the under pressure problem of the spring cone crusher was solved and today the cone crusher is one of the most efficient crushing machines.
The first hydraulic cone crusher was developed in 1948 by an American company. This cone crusher is able to expel some uncrushable materials that have somehow entered the crushing chamber and its discharging gap is adjustable. Until 1970s, an automatic controller was developed and featured in the hydraulic cone crusher. This was only the beginning. Through the following years, the cone crushers was significantly improved in all terms; efficiency, features, technologies, energy consumption, maintenance costs, etc.
Today, there are many different types of cone crushers, of which every type is most suitable for a specific range of applications and materials. The importance of this type of crushing machine has significantly increased, because of its effectiveness and surprisingly low operating costs. The cone crusher is able to crush hard, medium-hard and many different types of materials, while providing a reliable and efficient crushing operation. When compared with the jaw crusher, the cone crusher has a more stable structure, higher efficiency, economical operation and is adjustable, unlike the jaw crusher. Flexible and efficient, the cone crusher is widely utilized in many various industries.
12:04 AM
Mobile Crushers Are On The Move
Tuesday, July 1, 2014
Mobile crushers are making they breakthrough, as they are increasingly more utilized than few years ago. They offer the advantage of combining few crushing stages in one, while providing the ability to be easily transported from one job site to another.
Click here to read more:
http://www.everysingletopic.com/mobile-crushers-are-on-the-move/
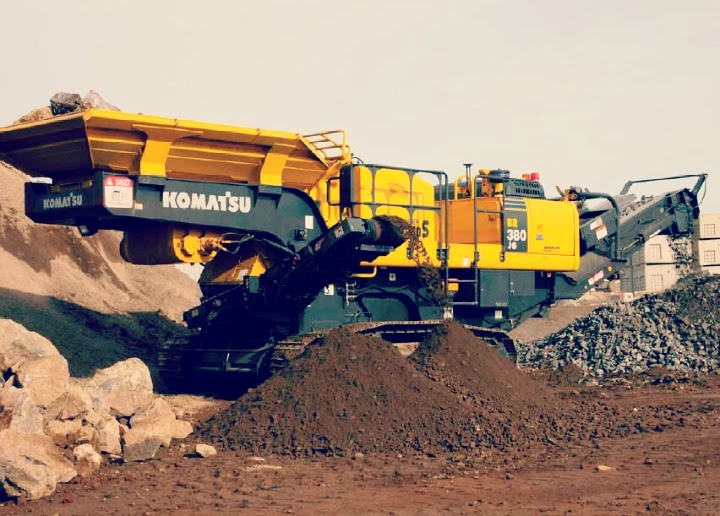
Click here to read more:
http://www.everysingletopic.com/mobile-crushers-are-on-the-move/
12:07 AM
How Is Technology Helping The Mining Companies
Monday, June 23, 2014
The latest technologies improve the efficiency and productivity in any industry, especially in the mining industry. With improved mining machines and implementing the latest technologies, the mining companies can have their productivity levels higher than ever.
Click here to find few key technologies that can certainly help the mining companies:
http://www.trendhunter.com.au/how-is-technology-helping-the-mining-companies/
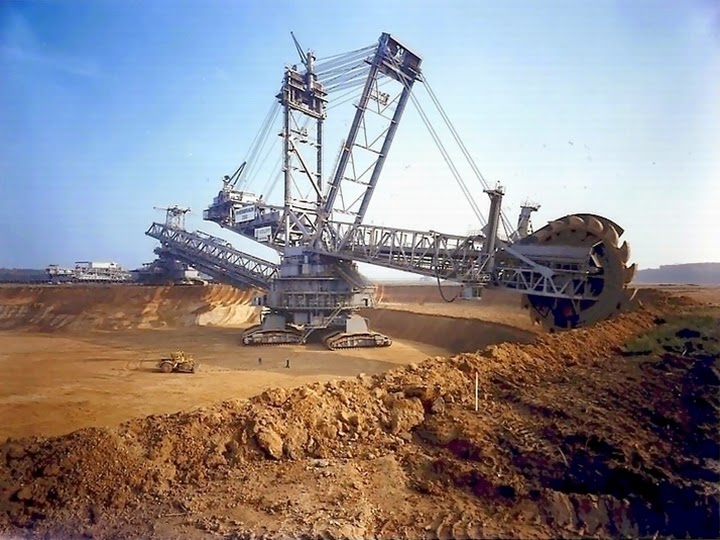
Click here to find few key technologies that can certainly help the mining companies:
http://www.trendhunter.com.au/how-is-technology-helping-the-mining-companies/
4:38 AM
Site grading is a methodology of changing slant and lifting the dirt around a building with a particular machine called grader. A grader is a piece of development gear that is greatly imperative in the development business and it is utilized to level uneven surfaces and to give a specific degree. With a huge, overwhelming cutting edge, the grader machine can cut the hardest materials in ground and its size and stature could be balanced by the administrator. Prior to any development transform, the site grading is obliged to even the surface and give a strong establishment to the home or building. Likewise, site grading may be performed for existing structures to enhance the seepage and make the wanted appearance.
Caterpillar has as of late presented the four models of K Series graders, which are supposed to totally supplant the well-known H Series. The H Series graders were utilized as a part of a mixed bag of provisions, incorporating in substantial development, way building and mining requisitions. The Caterpillar K Series graders will proceed the custom, as they gimmick a mixture of vital client prerequisites and staggering enhancements. They were particularly created to help any Cat client, while keeping up the noteworthy unwavering quality and high caliber of Cat graders.
Komatsu is a Japanese producer of mining, military and development supplies, with a knowledge of in excess of 95 years. Graders are surely amongst the best results of Komatsu, as they are broadly generally acknowledged. The most prominent Komatsu graders are Gd555, Gd655 and Gd675, which all fit in with the medium grader-class and gimmick a cutting edge 3.7 meters in length. These three Komatsu graders were presented in 2001 in North America and rapidly got exceptionally prevalent all as far and wide as possible. In the late years, numerous enhancements have been made and the Komatsu graders have got considerably more proficient.
Caterpillar or Komatsu Graders
Thursday, June 5, 2014
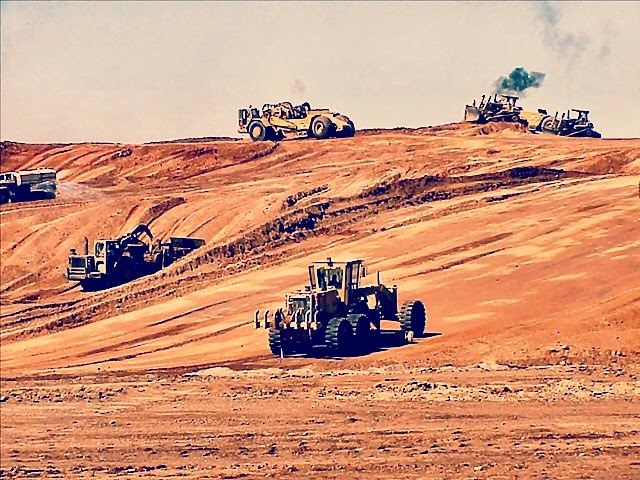
Caterpillar has as of late presented the four models of K Series graders, which are supposed to totally supplant the well-known H Series. The H Series graders were utilized as a part of a mixed bag of provisions, incorporating in substantial development, way building and mining requisitions. The Caterpillar K Series graders will proceed the custom, as they gimmick a mixture of vital client prerequisites and staggering enhancements. They were particularly created to help any Cat client, while keeping up the noteworthy unwavering quality and high caliber of Cat graders.
Komatsu is a Japanese producer of mining, military and development supplies, with a knowledge of in excess of 95 years. Graders are surely amongst the best results of Komatsu, as they are broadly generally acknowledged. The most prominent Komatsu graders are Gd555, Gd655 and Gd675, which all fit in with the medium grader-class and gimmick a cutting edge 3.7 meters in length. These three Komatsu graders were presented in 2001 in North America and rapidly got exceptionally prevalent all as far and wide as possible. In the late years, numerous enhancements have been made and the Komatsu graders have got considerably more proficient.
Subscribe to:
Posts (Atom)