Bobcat is a leading industry
manufacturer and world-known brand that produces high quality,
durable and powerful loaders. The brand also offers loader
attachments that can be matched with more than 60 different
applications. Loader attachments are designed and manufactured to
perfectly fit the base machine, which optimizes job performance,
dependability and durability. Fast and secure loader attachments
change is guaranteed by an exclusive mounting system. Loader
attachments even add more versatility when used with Bobcat loaders.
Here are some of the more commonly used Bobcat loader attachments.
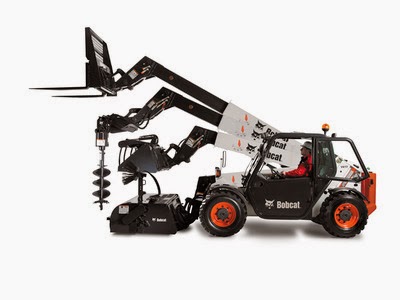
Backhoe attachment - With a backhoe
attachment you will be able to transform your bobcat loader into a
powerful excavator. With a full line of models, backhoe attachments
can be fitted with any Bobcat loader size. Perfect for tasks such as
landscaping, nursery sites, water and power maintenance lines, etc,
Bobcat backhoe attachment due to its minimal ground disturbance
operation, is also ideal for work in sensitive areas. The backhoe
attachment can be switched easy and fast. Its unique mounting system
maximizes the performance and minimizes the downtime.
Bucket Construction/Industrial - Fair
cutting edge visibility and excellent bucket breakout force are just
some of the features offered by construction and industrial buckets
in order to guarantee better digging and easier bucket filling. It is
an ideal loader attachments for tough digging and material handing.
Bucket (Rock) - Bucket (rock) is
designed for tough working conditions, and its tines are designed to
provide strength and durability. Ideal for contractors and
landscapers who want to separate unnecessary objects, like rocks and
debris while leaving finer material behind on the job site.
Grapple (Industrial) - Developed for
maximum power and reliability. The two-arm design provides strong,
even biting force. It can handle onto the toughest materials in the
industrial or construction setting. Easy operation and secure handle
bulk and uneven loads are allowed by its hydraulic controls. The
versatility on choosing a bucket or a fork bottom will maximize load
capability.
Grapple (Root) – This type of grapple
is designed to perform a smooth, yet strong operation with maximum
chomping and ripping power to complete even the toughest jobs. Also
with its specific tooth design, materials can be picked without
driving the teeth into the ground. Ideal for landscaping, demolition,
construction and grounds maintenance.
With the versatility of Bobcat loader
attachments, you will be able to grow you business, replace
non-efficient machines and have the necessary tools to accomplish
major projects.