The graders are heavy-duty machines
which are used for a variety of applications. In my opinion, these
machines are generally used for new road construction projects, when
flat and smooth surface base needs to be prepared. A motor grader is
a extremely versatile machine, capable to work with different
attachments for performing simple or delicate tasks.
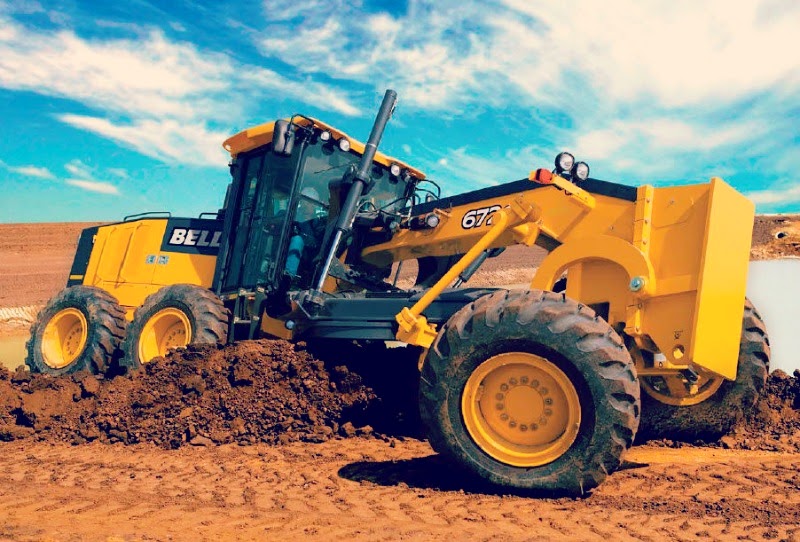
Click here to
learn more about the graders.